- Home
- Publications library
- Case Studies: Localising Redevelopment in London and Rotterdam
Case Studies: Localising Redevelopment in London and Rotterdam
The Centre for Liveable Cities visited the King’s Cross area in London and the Innovation Centre at the Former Shipyard of the Rotterdam Drydock Company (RDM) to learn about the innovative urban adaptations of these former disused spaces.
This article has been migrated from an earlier version of the site and may display formatting inconsistencies.
The Centre for Liveable Cities visited the King’s Cross area in London and the Innovation Centre at the Former Shipyard of the Rotterdam Drydock Company (RDM) to learn about the innovative urban adaptations of these former disused spaces.
Hotel above the 1856 St Pancras Eurorail station
King’s Cross London
Sitting on a 67-acre (27ha) plot in central London, King’s Cross is being redeveloped by King’s Cross Central Limited Partnership (KCCLP) . The teardropshaped site approximately 4km north of Charing Cross and 4.5km northwest of Liverpool Street, slopes upwards from Euston Road, with the Regent’s Canal running through it.
The area used to be where goods from other parts of UK were unloaded by rail, but as air cargo became more prevalent in the 1970s, the manufacturing industry moved out to cheaper locations as raw materials were transported via the road to them instead. Faced with less trade, rail operations ceased in the 1980s. Architect Norman Foster suggested tearing down all the buildings for new developments, but this did not materialise.
12 EDGE participants visit Ms Foo Chi Hsia, Singapore High Commissioner to United Kingdom of Great Britain and Northern Ireland.
Instead, there was an impetus to develop the area when it was announced in 1997 that the Eurostar station would be relocated to King’s Cross. This was further sustained by the 2005 announcement that London would be hosting the Olympics in 2012. One of the critical tasks at that time was to improve the image of this region.
This urban rejuvenation was made possible by the strong collaboration between the local planning authorities and the developer. This allowed the master plan to be kept flexible so the type of use could be adjusted in response to the changing economic conditions over time. This was especially critical as the development for the entire site was expected to last till 2024 to 2025. The master plan was also implemented in phases for financial viability, as the returns from the initial phases were used for development of subsequent phases.
Disused gas holders turned into housing
On the ground, investments were made to remediate the contaminated land and to improve infrastructure in the estate. To preserve the history and character of the estate, some disused buildings were carefully restored and put to adaptive use, while historical buildings were preserved and integrated with the rejuvenation plans. As part of a plan to engage the community, efforts were made to offer skills training in the form of local apprenticeships as well as job matching between the residents and businesses in the neighbourhood. During the construction phases, public access routes were made available so the community could walk the grounds and witness the transformation for themselves. All these initiatives helped enhance the residents’ sense of belonging to the area and improve the overall living environment.
Once seen as an unsafe and derelict old industrial district, the King’s Cross area today is a vibrant centre for commercial activities and the creative industries. Its public spaces are popular and well-utilised, and the area houses institutions such as the Central Saint Martins of the University of the Arts London (UAL). Even amidst the transformation, the district has retained its historical significance and character through the preservation of the façades of old buidings where possible and repurposing heritage buildings, such as turning the iconic gas holders into high-end housing. The area remains open, functional and accessible to public even as construction works continues to take place in large land plots in the area.
Attractive open spaces along canal
Gas holders transformed into a park
The old building façade preserved
Innovation Centre at the Former Shipyard of the Rotterdam Drydock Company (RDM)
The Rotterdam Drydock Company was a shipbuilding and repair shipyard built in 1902. In its heyday, it employed 7,000 workers until shipyard activities ceased in the late fifties and early sixties due to the emergence of cheaper shipyards in other parts of Europe and the Far East. It was left unmanned and began housing illegal drug activities until the Rotterdam Port Authority bought over the yard in 2002. They converted it into RDM in 2009, an innovative cluster that hosts a combination of spaces for business, education and events.
Image of 3D printed salt stool (left) and 3D printed heritage replica
RDM aims to be an innovation and education hub for the port industry in the following areas:
Maritime and smart port industry
Logistics and future mobility
Energy and processing industry
Sustainable building and innovative development
One of the impetus to establish RDM was because students were unable to find a job that matched their education. The solution was to form community of practices between schools and businesses solve industry challenges. For instance, Shell worked with RDM on a project looking at alternative forms of energy to fossil fuel. In such partnerships, companies fund close to 75% of the collaboration and retain intellectual rights of the outcomes.
Establishing RDM was challenging at the beginning due to its location away from the city. Efforts were made to improve connectivity, including introducing a water taxi that cut the traveling time between the city and the port area from an hour to 20 minutes. As global companies and projects such as artist Daan Roosegaarde’s smog free tower developed in RDM, the area gradually gained traction for fostering an innovative culture. Today, its home to a variety of collaborative projects including developing better glue technology to replace welding, and test-bedding concept houses that offer new ways of living and building, including through prefabrication, solar panel rooftops and interactive screens that monitor air quality.
To ensure RDM stays true to its goal of being a healthy environment for start-ups, companies and schools, companies interested in renting a space are evaluated based on the degree of innovation of the idea and safety risks posed. The space also houses a mix of educational institutions, ranging from higher level education institutes to middle level technical schools that equip students with technical skillsets. These policies ensure there is a diverse group of stakeholders who offer different ways of thinking.
In addition, start-ups have access to expensive equipment through a Makerspace area that offers shared industrial production facilities such as drones, 3D printers, robot arms, and laser cutters. Together, companies at the innovation dock have pooled their knowledge to tweak a more precise 3D printing process. Not only can they 3D print a salt stool and a replica of a heritage site that was destroyed by terrorists, RDM can manufacture and customise a 3D printed propeller faster than the traditional ways of casting in metal. This gives start-ups supporting Rotterdam’s shipping activities a competitive edge.
Other innovations at RDM include the aqua dock, which can generate waves that mimic real situations at sea for testing test floating projects, new ship models and submarine drones. The innovation dock allows for new building technologies to be tested, including a customised and precise robotic printing techniques for creating a self-supporting structure that does not require the support of glue, screws or additional materials. Recently, a robot cleaner was also successfully test bedded in RDM to clear trash at the port area.
About the Writer
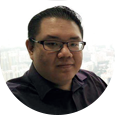
Joshua Sim
Joshua Sim is a researcher, writer and project manager at the Centre for Liveable Cities. He works with a passionate team on CLC’s monthly newsletter Better Cities. He has also written research pieces and articles for CLC’s bi-annual magazine Urban Solutions.